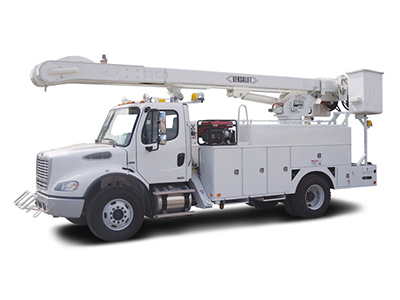
Annual inspection of Digger Derricks and Aerial Devices are essential acts not only to adhere to OSHA or ANSI requirements but to ensure the equipment is safe to use. A thorough inspection must be applied to all system components of the device. Although user manuals specify the components to be checked, a certified technician with adequate training, knowledge, and competitive experience is essential to ensure a comprehensive inspection.
If you're an owner and you choose to perform you own annual inspections, just know that you are likely to miss or overlook critical items that professional inspectors are trained to focus upon. Here is some list of most frequently overlooked items:
Overlooking Safety/Operational Labels
Operational and Safety labels provide significant details to users. The decals attached to the equipment might be damaged or removed from power washing over time. You are likely to miss a component if the decals are no longer in place. Hand signal charts must not be omitted from digger derricks. They provide an important function in the communication between operator and ground personnel, especially in a loud setting. Potential injury or damage in equipment is imminent if there's a failure to convey directions clearly.
Poorly Maintained Hydraulic Oil Levels and Hydraulic Filters Are Not Replaced
Hydraulic oil levels must be maintained based on the manufacturer's recommendation in order for the equipment to run seamlessly. If it reaches a low level but left unattended, it could lead to untimely costly repairs. It could initially cost you $2,000 repair for burning up one pump. Aside from that, you should also consider the deficit due to the equipment being removed from service.
Meanwhile, you should not check the fill levels when the outriggers are extended for it can concur to overfilling. When the system is overfilled, the space is no longer enough for expansion. This can add up to oil leakage. Moreover, a dirty oil filter can expedite the deterioration of the key components including pumps, hydraulic valves, cylinders, and hoses. This is because the filter is no longer efficient in trapping debris and contaminants prevalent in the fluid.
Defective Winch Rope
The winch rope should also be unwound and checked by hand at the yearly inspection. If you notice cuts or feel a bulge, this indicates an internal rope damage which is an outcome of shock loading or kinking. This means the rope must be replaced. Rope manufacturers provide more scrutiny and replacement conditions.
Torqued Rotation Bearing Bolts
This is an important item in the inspection list that should not be missed. Two personnel must do the checking so one may rotate the bearing while the other one inspects the bolt torque. Proper bolt torque and greasing must be done. Otherwise, it could result in failure of bearing bolt because the rest of the fasteners are overloaded. Repairs related to bearing failure could cost you up to $10,000.
Bearing Deflection/Backlash Has Too Much Allowance
Inspecting the allowance in the rotation bearing takes a while to master and requires clear insight on how to measure it. Too much allowance could indicate rotation bearing is worn and requires replacement. Furthermore, it may also hint that the boom has been shock loaded.
Leveling Chain Is Too Loose
Aerial devices' leveling chain must have precise amounts of preload. Potential wear and tear can increase when there's too much or too little tension. Inspecting the leveling tension needs removing off the boom lid. When the chain is not kept within tolerance, it may impact the self-leveling of the bucket when the booms motion through their range of motion.
Bucket and Liner Wear and Tear
The structural integrity of the bucket is damaged when there are cracks and distortions noted. A damaged liner can add up to the diminishing dielectric strength. Most of the time, inspectors fail to take off the liner when checking the bucket. Tools can drop and damage the liner, even the bucket. So make sure to check inside and outside the bucket and include underneath it.
Although carrying out the task on your own may appear as an affordable option, it is highly recommended to seek certified technicians who are experts in this field. If you are looking for a certified company who can conduct dielectric testing and inspection, contact ETS Inspection and Testing Services.