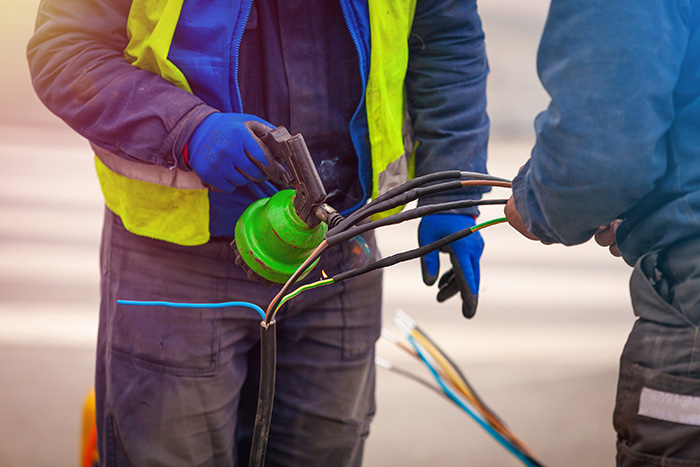
When laying underground high voltage cable systems, one must understand the criticality of cold shrink and heat shrink tubing. These tubing are used for splicing, terminating and serves as an environmental seal on LV (Low-Voltage) and MV (Medium-Voltage) cables. These two types of tubes look similar on the outside but have different internal characteristics. They have different applications, installation techniques and physical properties.
Heat-Shrink Tubing is a pre-stretched shrinkable plastic tube that requires a heat source during installation. It contains a polyolefin material that is contracted to form an environmental seal protection to the joint or cable. It is ideal for industrial or commercial projects that require a chemical-resistant tubing and when serving low temperature environments.
Cold-Shrink Tubing is a factory-expanded rubber sleeve with an open end and assembled onto a supporting removable plastic core. Cold shrink tubing is installed by applying a gentle unwinding motion to release it from the core. It offers a quicker and safer installation process as compared to heat shrink tubing installation.
Cold shrink tubing is the preferred material for insulating wires, terminals, joints and connections in electrical work. You may also use it when repairing bundle of wires together and as a protection for small wires from minor abrasion. It requires to be stored in a controlled setting wherein temperature does not go beyond 43 degrees Celsius.
Both heat-shrink and cold-shrink splicing is an important step to protect spliced cables from environmental elements that may ingress within. It is an essential part of distribution circuits and DSS line re-conductoring for capacity works.
For more information about underground high or low voltage installation, contact ElecComm.